Here is a detailed explanation on types of variable speed drives, including their construction, working principles, advantages, disadvantages, and applications.
Variable Speed Drives (VSDs), also known as Variable Frequency Drives (VFDs) or Adjustable Speed Drives (ASDs), are devices or systems used to control the speed and torque of motors by varying the frequency, voltage or power supplied to the motor.
They are widely used in industrial, commercial, and residential applications to improve energy efficiency, enhance process control, and reduce mechanical stress on equipment.
What is a Variable Speed Drive?
A Variable Speed Drive (VSD) is a device or system that controls motor speed and torque by adjusting the power supplied to it. Unlike fixed-speed motors, VSDs enable motors to operate at varying speeds, enhancing efficiency, performance, and energy savings.
VSDs can be electronic, mechanical, or hydraulic, depending on the control method used. By optimizing motor speed, they improve process control, reduce wear and tear, and lower energy consumption compared to traditional fixed-speed systems.
They are especially beneficial in applications with variable loads, such as pumps, fans, conveyors, and compressors, where adjusting motor speed to match demand significantly enhances efficiency.
Types of Variable Speed Drives – VSDs
There are several types of variable speed drives, each with its own unique characteristics and applications. The most common types include:
1. AC Drives (Variable Frequency Drives – VFDs)
Working Principle:
AC drives control the speed of AC induction motors by converting incoming AC power to DC power and then inverting it back to AC at a variable frequency and voltage. This variation in frequency regulates the motor speed effectively.
Advantages:
- High energy efficiency
- Precise speed control
- Reduced mechanical stress on equipment
- Soft starting capabilities reduce electrical surges
Disadvantages:
- Higher initial cost
- Requires proper filtering to minimize harmonics
- Can be complex to configure and maintain
Applications:
- Pumps and fans
- Compressors
- Conveyors
- HVAC systems
2. DC Drives
Working Principle:
DC drives regulate the speed of DC motors by varying the voltage supplied to the motor. By adjusting the voltage, the motor speed can be increased or decreased efficiently.
Advantages:
- Simple control mechanism
- High starting torque
- Cost-effective for low-power applications
Disadvantages:
- Requires regular maintenance (commutator and brushes)
- Less efficient compared to AC drives
- Limited availability of DC motors compared to AC motors
Applications:
- Cranes and hoists
- Elevators and lifts
- Traction systems (electric trains, trolleys)
3. Eddy Current Drives
Working Principle:
Eddy current drives control motor speed using a magnetic field. A fixed-speed motor is coupled with an eddy current clutch, which modulates torque transmission and adjusts the output shaft speed.
Advantages:
- Simple design with minimal wear and tear
- Smooth speed variation without electrical components
- Low maintenance requirements
Disadvantages:
- Lower efficiency compared to electronic drives
- Limited speed control range
- Generates heat, requiring additional cooling
Applications:
- Conveyors
- Mixers and agitators
- Winders and rolling mills
4. Hydraulic Drives
Working Principle:
Hydraulic drives use pressurized fluid to control motor speed. A hydraulic pump delivers fluid to a hydraulic motor, where the flow and pressure determine the speed and torque output.
Advantages:
- High torque output
- Suitable for heavy-duty applications
- Smooth and stepless speed control
Disadvantages:
- Requires regular maintenance due to fluid leaks
- Lower efficiency due to energy losses in fluid transmission
- Sensitive to temperature changes affecting fluid properties
Applications:
- Heavy machinery (excavators, bulldozers)
- Presses and stamping machines
- Winches and lifting systems
5. Mechanical Variable Speed Drives
Working Principle:
Mechanical VSDs use mechanical components such as belts, pulleys, gears, and variable-speed couplings to adjust motor speed without electrical intervention.
Advantages:
- Simple and cost-effective
- Reliable with minimal electronic interference
- No need for external power control
Disadvantages:
- Limited speed control precision
- Higher wear and tear on mechanical parts
- Lower efficiency compared to electronic drives
Applications:
- Machine tools
- Conveyor systems
- Industrial mixers and agitators
Types of Variable Frequency Drive (VFD)
VFDs control motor speed, enhancing efficiency and performance in various applications. Choosing the right type depends on cost, efficiency, and application needs.
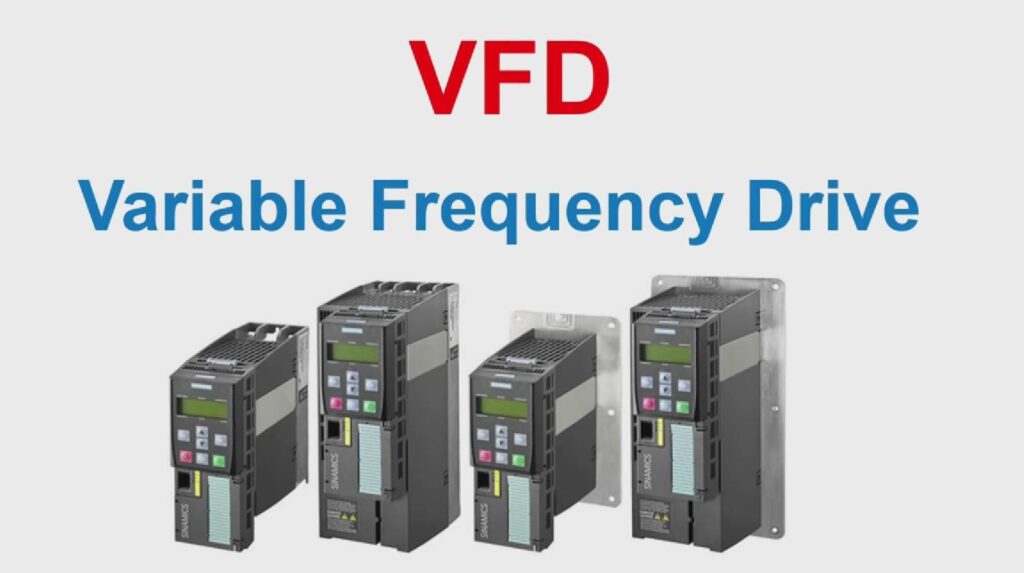
1. Voltage Source Inverter (VSI) Drives
- Cost-effective, efficient, widely used
- Poor low-speed performance, higher harmonics
- Applications: Fans, pumps, HVAC
2. Current Source Inverter (CSI) Drives
- High torque at low speeds, reliable
- Expensive, bulky
- Applications: Mining, steel mills, compressors
3. Pulse Width Modulation (PWM) Drives
- High efficiency, precise control
- High initial cost, requires filtering
- Applications: Robotics, material handling
4. Direct Torque Control (DTC) Drives
- Best speed/torque control, fast response
- Expensive, complex
- Applications: Automation, wind turbines
5. Multi-Level Inverter Drives
- Low harmonics, high efficiency
- Expensive, complex
- Applications: Power generation, large-scale systems
6. Volts/Hertz (V/Hz) Control VFDs
- Simple, cost-effective
- Limited precision
- Applications: Pumps, HVAC
7. Sensorless Vector Control VFDs
- Good torque control, no encoder needed
- Complex tuning
- Applications: CNC machines, cranes
8. Flux Vector Control VFDs
- Superior precision, fast response
- Expensive, needs sensors
- Applications: Robotics, printing
9. Matrix Inverter VFDs
- High efficiency, low harmonics
- Expensive, complex
- Applications: Renewable energy, aerospace
Choosing the Right VFD
- Cost-sensitive: VSI, V/Hz, PWM
- High torque: CSI, DTC
- High precision/power: Multi-level, Flux Vector, Matrix
Construction of Variable Speed Drives
The construction of a Variable Speed Drive (VSD) depends on its type electronic, mechanical, or hydraulic. However, most modern VSDs are electronic and primarily consist of power electronics and control systems. Below is a general breakdown of the construction of electronic VSDs (specifically Variable Frequency Drives, VFDs).
1. Rectifier
- The rectifier is the first stage of a VSD and is responsible for converting the incoming AC power to DC power. In AC drives, the rectifier typically consists of diodes or thyristors that allow current to flow in only one direction.
2. DC Bus
- The DC bus is an intermediate stage that stores the DC power generated by the rectifier. It typically includes capacitors that smooth out the DC voltage and reduce ripple.
3. Inverter
- The inverter is the final stage of a VSD and is responsible for converting the DC power back to AC power at a variable frequency and voltage. The inverter typically uses insulated gate bipolar transistors (IGBTs) to switch the DC power on and off rapidly, creating a simulated AC waveform.
4. Control Unit
- The control unit is the brain of the VSD and is responsible for controlling the operation of the rectifier, DC bus, and inverter. It receives input signals from the user or process control system and adjusts the output frequency and voltage accordingly.
5. Cooling System
- VSDs generate heat during operation, so they are typically equipped with a cooling system to dissipate the heat and prevent overheating. The cooling system may include fans, heat sinks, or liquid cooling.
6. Input & Output Filters
- Filters (chokes or reactors) reduce electrical noise (harmonics) and protect the motor.
- Ensures smoother power delivery.
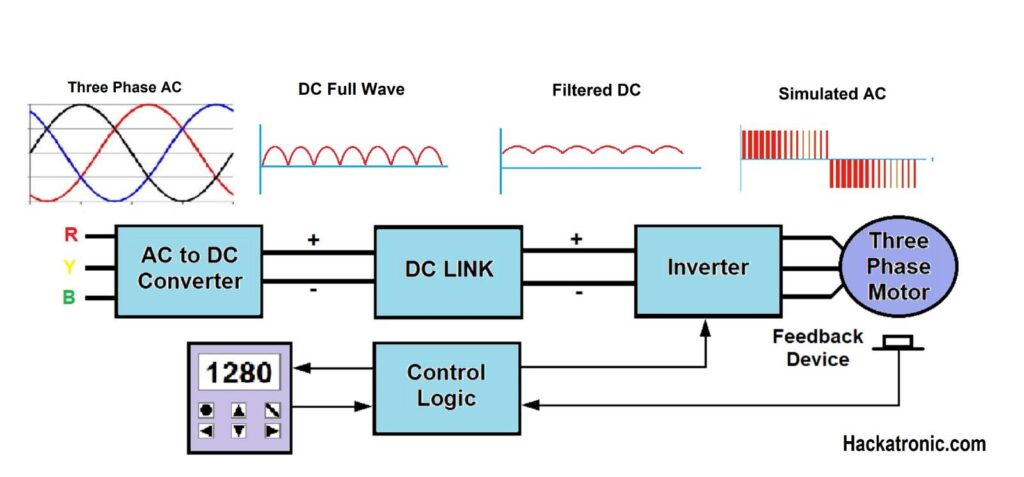
Working of Variable Speed Drives
Different types of variable speed drives have their own working methods. Here we will see the working of an AC variable speed drive (VFD).
- Rectification:Â The incoming AC power is converted to DC power by the rectifier. The rectifier allows current to flow in only one direction, creating a pulsating DC voltage.
- Smoothing:Â The pulsating DC voltage is smoothed out by the capacitors in the DC bus, creating a stable DC voltage.
- Inversion:Â The DC voltage is converted back to AC power by the inverter. The inverter uses IGBTs to switch the DC voltage on and off rapidly, creating a simulated AC waveform with a variable frequency and voltage.
- Control:Â The control unit adjusts the frequency and voltage of the AC power supplied to the motor based on input signals from the user or process control system. By varying the frequency and voltage, the control unit can adjust the speed of the motor to match the load requirements.
- Output:Â The variable frequency and voltage AC power is supplied to the motor, which adjusts its speed accordingly.
- Feedback: A feedback loop is used to monitor and adjust motor performance dynamically. Feedback can be a voltage, current or speed.
Advantages of Variable Speed Drives
Variable speed drives offer several advantages over traditional fixed-speed motor control methods, including:
1. Energy Savings
- VSDs can significantly reduce energy consumption by adjusting the motor speed to match the load requirements. This is particularly beneficial in applications where the load varies over time, such as in pumps, fans, and compressors.
2. Improved Process Control
- VSDs provide precise control over motor speed, allowing for better process control and improved product quality. This is especially important in applications such as conveyors, mixers, and extruders.
3. Reduced Mechanical Stress
- By gradually ramping up the motor speed, VSDs can reduce mechanical stress on the motor and driven equipment, leading to longer equipment life and reduced maintenance costs.
4. Soft Start and Stop
- VSDs provide a soft start and stop function, which reduces the inrush current and mechanical shock associated with direct-on-line starting. This can help to extend the life of the motor and reduce wear and tear on mechanical components.
5. Power Factor Correction
- VSDs can improve the power factor of the motor, reducing the reactive power demand and improving the overall efficiency of the electrical system.
Disadvantages of Variable Speed Drives
Despite their many advantages, variable speed drives also have some disadvantages, including:
1. Initial Cost
- VSDs can be expensive to purchase and install, particularly for large motors. However, the energy savings and other benefits often outweigh the initial cost over time.
2. Complexity
- VSDs are more complex than traditional fixed-speed motor control methods, requiring specialized knowledge for installation, programming, and maintenance.
3. Harmonic Distortion
- VSDs can generate harmonic distortion in the electrical system, which can cause problems such as overheating of transformers and capacitors, and interference with other electronic equipment. Harmonic filters may be required to mitigate these issues.
4. Heat Generation
- VSDs generate heat during operation, which can reduce their efficiency and lifespan if not properly managed. Adequate cooling and ventilation are essential to prevent overheating.
5. Electromagnetic Interference (EMI)
- VSDs can produce electromagnetic interference (EMI), which can affect nearby electronic equipment. Proper shielding and grounding are necessary to minimize EMI.
Applications of Variable Speed Drives
Various types of variable speed drives are used in a wide range of applications across various industries, including:
1. Pumps
- VSDs are commonly used in pump applications to control the flow rate and pressure of liquids. By adjusting the motor speed, VSDs can match the pump output to the system requirements, reducing energy consumption and improving process control.
2. Fans
- VSDs are used in fan applications to control the airflow and pressure in HVAC systems, industrial ventilation, and cooling towers. By adjusting the fan speed, VSDs can optimize energy efficiency and reduce noise levels.
3. Compressors
- VSDs are used in compressor applications to control the output pressure and flow rate of compressed air. By adjusting the compressor speed, VSDs can match the air demand, reducing energy consumption and improving system efficiency.
4. Conveyors
- VSDs are used in conveyor systems to control the speed of the conveyor belt, allowing for precise control of material handling and reducing wear and tear on the conveyor components.
5. Machine Tools
- VSDs are used in machine tools to control the speed of the cutting tools, allowing for precise control of the machining process and improving product quality.
6. Extruders
- VSDs are used in extruder applications to control the speed of the screw, allowing for precise control of the extrusion process and improving product consistency.
7. Cranes and Hoists
- VSDs are used in cranes and hoists to control the speed of the lifting mechanism, allowing for precise control of the load and reducing mechanical stress on the equipment.
8. Renewable Energy
- VSDs are used in renewable energy applications such as wind turbines and solar tracking systems to optimize the performance of the system and improve energy efficiency.
Conclusion
There are different types of variable speed drives with versatile and powerful features that offer significant benefits in terms of energy savings, process control, and equipment longevity. While they come with some challenges, such as initial cost and complexity, the advantages they provide often outweigh the disadvantages, making them an essential component in modern industrial and commercial applications.
Understanding these types of variable speed drives helps in selecting the right motor drive system to maximize efficiency, minimize costs, and enhance overall performance.
As technology continues to advance, variable speed drives are likely to become even more efficient, reliable, and cost-effective, further expanding their range of applications and contributing to a more sustainable and energy-efficient future.