To meet customer demands without skyrocketing costs, many companies have turned to lean manufacturing. Electronics manufacturing is all about keeping things efficient and high-quality. This has to be consistent with new devices constantly being developed.
What Is Lean Manufacturing?
The lean manufacturing strategy is focused on cutting waste and boosting productivity. It helps electronics manufacturers do the following:
- Streamline processes
- Minimize downtime
- Reduce material costs
What Lean Manufacturing Means for Electronics?
Originally, lean manufacturing was a big deal in the automotive industry. Surprisingly, it’s proven to work well in EMS manufacturing too. The whole idea is to improve the process at every stage, making things faster, cleaner, and less expensive.
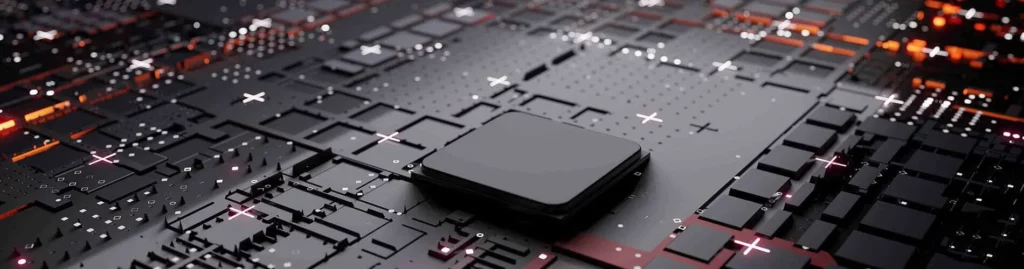
There are five core principles in lean manufacturing:
- Value
- Value stream
- Flow
- Pull
- Perfection
These principles help companies focus on getting the product to the customer sans the extra costs or delays.
In electronics, lean can be super useful for trimming down on material waste, reducing production time, and maintaining high quality. Since tech products change so often, lean also helps companies stay flexible and ready to pivot when needed. Whether it’s managing inventory or adjusting production for a new device, lean helps keep things moving.
Lean Manufacturing Tools for Electronics:
Putting lean into action in electronics means using some specific tools and techniques. Here are a few popular ones and how they fit into this field:
Value Stream Mapping (VSM)
VSM maps out every step of the production process. From raw materials to the final product, it shows where time, effort, or money is being wasted. For electronics, VSM is perfect for spotting issues in assembly lines, testing steps, or supply chain slowdowns. Once you see the hold-ups, you can fix them to speed up production and reduce delays.
5S for Workplace Organization
The 5S system—Sort, Set in order, Shine, Standardize, and Sustain—keeps workspaces organized and efficient.
For electronics, particularly for busy operations like PCB fabrication, this could mean setting up specific areas for tools, components, and finished products to prevent a cluttered mess. When everything has its place, it’s easier to keep things efficient and in order.
Just-in-Time (JIT) Inventory
With JIT, parts are delivered exactly when they’re needed, not before. This helps electronics manufacturers avoid piles of unused parts sitting around. Working with suppliers to schedule deliveries based on demand helps keep inventory low. It also frees up space and saves money in the long run. Plus, it makes it easier to pivot quickly when product demands change.
Kaizen for Continuous Improvement
Kaizen is all about finding small ways to improve constantly. In electronics, Kaizen could mean simplifying assembly, speeding up testing, organizing circuit board design teams, or improving packaging. When every team member looks for ways to improve, the little changes add up. Kaizen events and suggestion boxes can make it easy for people to contribute, making small tweaks that collectively create a huge difference.
Automated Quality Control
Electronics need to be precise. Automated tools like Automated Optical Inspection (AOI) make it easier to catch defects in real-time. This helps eliminate issues right in the middle of production. Automated quality checks ensure that only reliable products make it to the end. Plus, this aligns with lean principles—fixing issues during the process instead of waiting for the final inspection.
The Challenges of Lean in Electronics:
While lean manufacturing is useful, putting it into practice in electronics has its own challenges:
Rapid Product Changes
Electronics products change fast. New models and updates are always in the works, which can mess with JIT inventory and standardized processes. To keep up, manufacturers can build systems that let them adjust production quickly and coordinate with suppliers for more flexible orders.
Complex Supply Chains
Electronics often require parts from suppliers worldwide, and any delay in the chain can throw off production. Maintaining lean principles with a complex supply chain is tough, but companies can build strong partnerships, use buffer stock for key parts, and monitor the supply chain in real time. This way, they can catch issues early and work around them.
Precision Requirements
Electronics parts are tiny and need to meet strict standards. Lean practices that focus on speed and efficiency can’t overlook the importance of quality control. Automated quality control is the answer here. Integrating these checks into production makes sure everything stays precise without sacrificing speed.
Why Lean Manufacturing Works in Electronics?
For electronics companies, lean manufacturing offers a bunch of perks:
Lower Costs: Lean trims down waste, rework, and excess inventory, making production cheaper.
Better Flexibility: Lean practices make it easier to shift production, update designs, or change product quantities based on demand.
Higher Quality: With continuous improvement and automated quality checks, lean helps minimize defects and create reliable products.
Faster Production: Smoother processes mean faster production, helping companies launch new products sooner.
PCB Fabrication Flowchart:
